What Plant Manager Needs to Know About Combustible Dusts
- Get link
- X
- Other Apps
By
Jeffrey C. Nichols
-
From our friends at Fauske:
By Zachary Hachmeister, Chief Operating Officer, Fauske & Associates, LLC5 Things Every Plant Manager Needs to Know About Combustible Dusts
Posted by
Zachary Hachmeister on 05.08.19
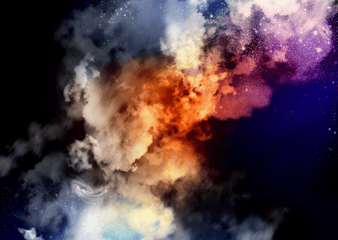
This may sound obvious, but it’s really important. You need to think of dust deposits on surfaces or dust leakage from equipment as uncontrolled fuel in your facility. This, of course, is only true for dusts that are combustible. The reason this is so important is that it will help shift you and your employees’ perspective on dust from a nuisance that reflects a lack of cleanliness to a potential hazard that is putting you, your co-workers, and your assets at risk. (This slight shift in perspective can translate to an increased awareness of combustible dust hazards and by doing so, can help you identify where dust is escaping from your process into your facility for better combustible dust control.)
Keep it Clean
If gasoline is spilled, there is an immediate hazard. Flammable vapors rapidly spread throughout the area and if they contact an ignition source, it is likely an explosion or flash fire will occur. If no ignition source is present though, the fuel evaporates and the flammable atmosphere dissipates until the hazard no longer exists. Solid fuels, like combustible dust are different in that they need to be physically removed. Hopefully this is accomplished through safe cleaning practices. However, if left untouched the material becomes susceptible to other means of dispersion that can lead to a catastrophic explosion.
Take Control at Transfer Points
The dust that has escaped the confines of your process, a.k.a. fugitive dust, typically originates from unconfined dust generating operations that are not properly ventilated. Transfer points in particular are susceptible as many processes use a series of conveyors, screws, and hoppers to move material from one part of the process to another. Often there is a short distance of free fall where the material is suspended as it changes elevation. Cutting and grinding operations are a couple of other common sources that come to mind as well. Enclosing, or partially enclosing and providing industrial ventilation for these dust generating operations can greatly reduce the amount of fugitive dust in your facility. Though the equipment comes at a price, a cost savings can also be recognized from the reduction in man hours needed for housekeeping activities.
Contain and Mitigate
Taking control of dust that is escaping your process through proper industrial ventilation design and employing good housekeeping measures to keep your facility clean can greatly reduce the risk of a catastrophic dust explosion that could compromise your entire facility. However, now that dust is contained to the system, proper mitigation of explosion hazards for these systems is imperative. Installing explosion protection equipment such as explosion relief venting, suppression, and/or isolation on equipment that handles combustible dust will further reduce the risk of injury or loss of assets. An example of typical equipment to focus mitigation efforts on includes dust collectors, cyclones, silos and spray dyers. The need for protection of industrial equipment is determined through the presence of sufficient quantities or dust, credible ignition sources, and credible dispersion mechanisms.
The Onus is on You
NFPA 652 Standard on the Fundamentals of Combustible Dust specifically states that the owner/operator is responsible for characterizing the combustible materials in their facility, identifying combustible dust hazards associated with those materials, mitigating identified hazards, and communicating these hazards to the workforce. Though NFPA is not an enforcement body, OSHA, fire marshals, building inspectors, and insurance underwriters do enforce NFPA standards.
Therefore, compliance with NFPA not only makes sense from a safety standpoint – it is expected by these governing bodies. Characterization of your materials is the first step in determining if you have combustible dust onsite. This can be accomplished by creating an inventory of your powdered materials and identifying which are combustible and which are not. A literature search of your materials can be used to identify known combustibles.
However, your most concrete evidence of combustible versus non-combustible will be generated through laboratory experiments conducted on representative samples of your materials.
A dust hazard analysis (DHA) per NFPA 652 can be employed to identify the combustible dust hazards that are present in your facility. Essentially, DHA is a documented systematic evaluation of each piece of equipment and building that handles or contains combustible dust to identify where these hazards exist. A proper DHA will review current administrative and engineering controls that are used to manage these hazards and offer recommendations to mitigate unsafe conditions. Take a look at FAI's three step approach to DHA by clicking the image below
- Get link
- X
- Other Apps
Comments
Post a Comment