Chemical safety best practices
From: Safety and Health Magazine
https://www.safetyandhealthmagazine.com/articles/21720-chemical-safety-best-practices
What are the best practices, and proactive measures being taken, to ensure chemical safety in the workplace?
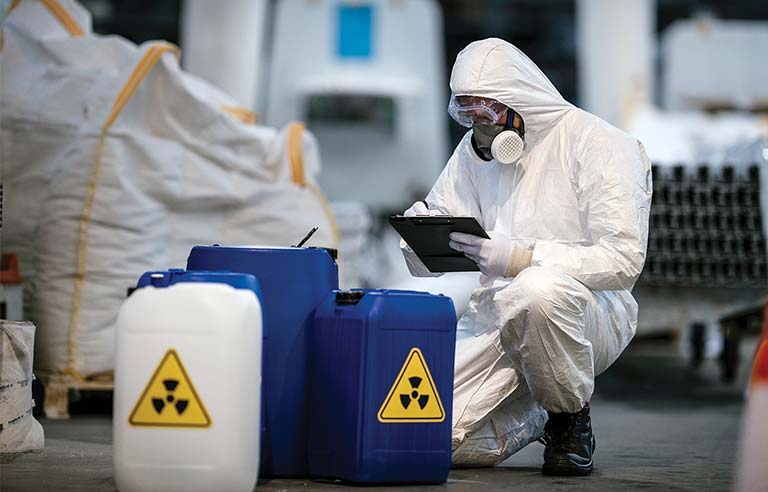
Responding is Sean Salvas, senior market strategy lead – EHS, Origami Risk LLC, Chicago.
Chemical safety practices in the United States have been steadily expanding over the years, especially after the 2012 adoption of elements of the United Nations’ Globally Harmonized System of Classification and Labeling of Chemicals into OSHA’s Hazard Communication Standard (1910.1200).
Notably, this action led to new hazard labeling requirements, the creation of the 16-section Safety Data Sheet format and new hazard classifications.
The UN has introduced subsequent editions of GHS yet to be adopted by OSHA. However, the agency’s latest proposal to update the Hazard Communication Standard with the seventh edition of the GHS will bring more changes, including:
- New hazard classification categories for aerosols, desensitized explosives and flammable gases, along with revised hazard and precautionary statements.
- New or revised definitions for combustible dust, gas, exposure or exposed, and other terms.
- The reconciliation of Hazard Communication Standard labeling requirements with those of the Department of Transportation, including streamlined labeling requirements for small chemical containers.
- Added concentration ranges on SDSs to help identify substances with formulations classified as confidential business information.
Besides ensuring compliance with globally accepted standards, the new requirements focus on human safety and health as well as preventing environmental damage.
Apart from the regulatory developments, organizations are proactively addressing all aspects of chemical use, including their manufacture, transport, use, handling, storage and disposal. Many are implementing best practices, including:
Establishing chemical standard operating procedures, which cover different aspects of chemical handling, such as delivery of raw materials, storage and disposal.
Routine inspections and maintenance, which keep organizations informed of potential chemical hazards and risk profiles.
Periodic hazard communication training, including instruction on safety protocols as well as drills to prepare for and respond to incidental chemical releases or related catastrophes.
Ensuring proper controls are in place, such as ventilation to pump out noxious gases, or being equipped with alarms and gas sensors to detect air toxicity levels, as well as the Hierarchy of Controls to eliminate hazards or apply appropriate safety measures where necessary.
Ensuring safe chemical storage, so chemicals are stored in appropriate containers and at correct temperatures and pressure levels, properly labeled, accessible yet well protected, and checked regularly.
Prioritizing asset maintenance, including keeping to routines to minimize risks of leaks or spills, and ongoing monitoring of equipment, pipes, storage containers and the environment to optimize chemical operations and ensure safety.
Performing assessments of personal protective equipment, including the evaluation of the integrity and use of all goggles, lab gowns, rubber gloves, hazmat suits and respiratory protection (self-contained breathing apparatuses, etc.) required for handling toxic and corrosive chemicals.
Establishing environmental protection measures, such as standard protocols for spills (including containment procedures) as well as staff training on first aid and emergency equipment such as fire extinguishers, drench showers and readily available first aid kits.
In addition to the various proactive safety measures adopted by industry, newly proposed regulations will help advance efforts to mitigate risks chemicals pose to employees, the public and the environment.
Comments
Post a Comment