Combustion concerns: Fume and dust management in grinding and welding operations
Combustion concerns
Fume and dust management in grinding and welding operations demand careful system designs
When collecting dust and fumes in a manufacturing environment, not only does the system you use have to draw harmful materials away from operators, it needs to do so in a manner that safely guards against the risk of explosions or fire in the dust or fume collector.
Weld fume rarely is explosive, but a lot of the weld fume is combustible; in other words, though it is at little risk of creating an explosion, there is a risk of starting a fire due to sparks entering the system.
Grinding, on the other hand, can create a very explosive dust, particularly if you are working in aluminum.
Grinding and weld fume require different approaches to fume management. Here’s what distinguishes each.
Grinding Requirements
The dust collection system for your grinding department should be separate to that used for welding. The combination of welding sparks and grinding dust has the potential to create an unsafe situation. Beyond that simple fact, the risks in the two processes are different.
The setup for your dust collector in the grinding department will depend on your processes. Generally, your extraction system could be a fixed hood, an extractor arm, or a slotted hood system at the back of each station. For certain types of tools, on-tool extraction can be used as well.
Whatever method you use, it’s critical to ensure that the system is adequate for the amount of dust you produce. The American Conference of Governmental Industrial Hygienists (ACGIH) and similar organizations offer recommendations for many applications and parameters on how to achieve that.
Once you have collected the dust at source, the transport velocity also is important. You have to make sure the dust is traveling through the ductwork and not falling in the midst of it, accumulating, and creating the risk of system failure.
In terms of the dust collector, it is useful to have your dust analyzed to determine its risk profile so that you know what you are dealing with. If it is explosive, you have to include countermeasures to address that risk. One important aspect is to isolate the ductwork so that if there is an explosion that originates in the dust collector, it doesn’t reverberate back into the building. Similarly, if there is an explosion vent, it’s important to make sure that the area where the fireball would be directed is closed off so people don’t congregate in that area.
Weld Fume Requirements
For weld fume extraction, there are a wide variety of options to ensure fume is kept away from the operator, from fume guns to extractor arms and fume hoods. Capture velocity is important to ensure you are drawing the fume at the correct rate without disrupting the shielding gas and weld quality.
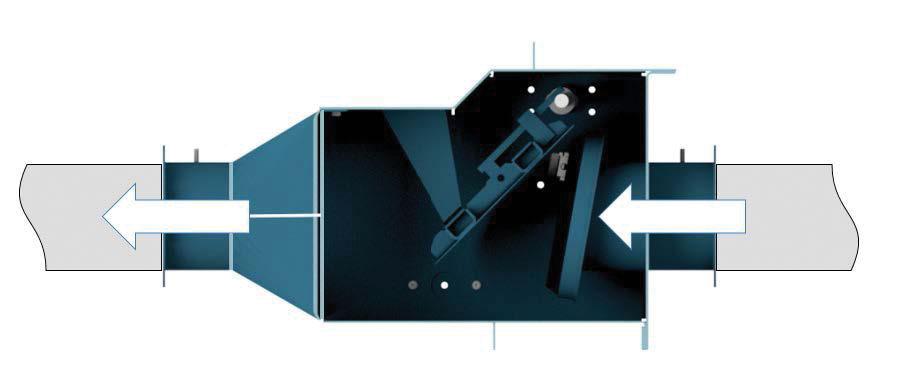
If you collect dust that is explosive, you have to include countermeasures to address that risk. One important aspect is to isolate the ductwork so that if there is an explosion that originates in the dust collector, it doesn’t reverberate back into the building. Here we see an illustration of an explosion isolation valve in a normal setting.
One of the key pieces of safety equipment to combat the fire in your extractor system is a spark arrestor. These tend to be built into most mobile collectors. Spark arrestors are designed to create a tortuous route for a spark to attempt to travel through. Anything with mass has momentum; a lot of spark arrestors create changes in direction so that a spark is somewhat heavy when it must do so, forcing it to run into a wall and fall out of the airstream, losing its momentum.
One of the last barriers before a spark can reach the dust collector are fire-retardant filter cartridges. While these filters don’t stop a fire from starting, they do minimize the risk of such a fire from spreading.
A lot of dust collectors now can be equipped with smoke detectors or IoT-based systems that monitor air stream temperatures that can alert you to a situation quickly, avoiding any other collateral damage possible with a dust collector fire.
IoT Support
Your dust or fume collector protects employees from hazardous fumes and dust created during your shop’s necessary operations. IoT-enabled collectors make it possible to track how well these systems are operating and mitigate the risk of system failures. These systems can be customized to collect the data you consider critical.
It makes sense to use this technology to track a variety of key factors. The first is an airflow sensor, which ensures that adequate airflow is being drawn through the system to achieve adequate capture velocity at the hood.
Associated with that is transport velocity, again particularly for combustible dust applications. If you know there’s a minimum amount of airflow required when you design the ducting system, properly monitoring that can ensure your airstream isn’t moving too slow, causing the dust to fall out, creating an unsafe situation.
If you are dealing with an explosive dust, you are going to have some kind of isolation valve near the collector. A dust accumulation sensor on that isolation valve can help alert you to problems between necessary physical valve inspections.
Sensors can be used at the collector to monitor a drop in filter pressure. Beyond that, you can monitor the amount of dust that accumulates in the hopper, drum, or drawer underneath the collector. Almost every company that has a dust collector has let it overfill or missed the maintenance window, creating a mess when emptying it. A sensor will tell you when to attend to it.
Another important consideration beyond safety and uptime is employee effectiveness. A lot of welders are responsible for dust collector maintenance; removing that responsibility from your welders is a definite advantage.
On the discharge side of the collector, emissions monitors can alert you if there is a leak in a filter or it is installed incorrectly.
It’s also possible to monitor fan vibration. One example where this can be of value is if you have a large central system with a big, custom fan. If that fan breaks down (because it is out of balance or has a catastrophic failure), lead times to get replacement parts can be a challenge. If you have a monitor that can alert you to a problem ahead of time, you can perform the necessary preventive maintenance, which could make a big difference in shop operations.
If a shop uses rotary airlocks, it’s possible to monitor that they are rotating and discharging dust. As mentioned previously, monitoring airstream temperatures can alert you to a fire risk. In a situation where you can’t go below a certain temperature, it can warn you of that as well.
Clean and safe shops are more likely to retain talented employees—a resource that is becoming harder to find all the time. Ensuring your dust or fume collector is designed to operate as effectively as possible is one way of helping maintain that clean and safe environment.
Travis Haynam is vice-president segments, extraction and filtration division, Nederman, 4404-A Chesapeake Drive, Charlotte, NC 28216, travis.haynam@nederman.com, www.nederman.com.
Don’t Forget Your Cobot!
A lot of companies are investing in cobots to address worker shortages. In many cases, they believe their workers are safer because the welder isn’t leaning into that weld fume.
However, that fume is still be created and must be managed. Amid the excitement to get the cobot operational, shops often overlook fume mitigation strategies. Even if your operations are within standards, if this isn’t addressed, the fume will build up on HVAC filters, accumulate on inventory, and decrease air quality unnecessarily.
Are Combustible Dust Explosions a Concern for Your Shop?
Most discussions surrounding weld fumes are focused on concerns about employee exposure and mitigating the hazards of that exposure. This is understandable; keeping employees healthy and comfortable in the workplace is key to maintaining and increasing productivity.
But other concerns related to weld fumes need to be taken into account. According to a new white paper produced by RoboVent, Sterling Heights, Mich., some shops also should review how combustible its weld fumes might be.
Most metal dusts are highly combustible, but the high heat of the welding process oxidizes most metal particulates. However, as the white paper points out, “more recent studies suggest that many weld fumes contain a mix of both oxidized and unoxidized particles of various sizes.” The composition and ratio of oxidized and unoxidized particles, along with the KSt value—which measures how fast the pressure rise occurs in an explosion—will determine the risk of a weld fume’s combustibility.
To download a copy of the study, visit www.robovent.com.
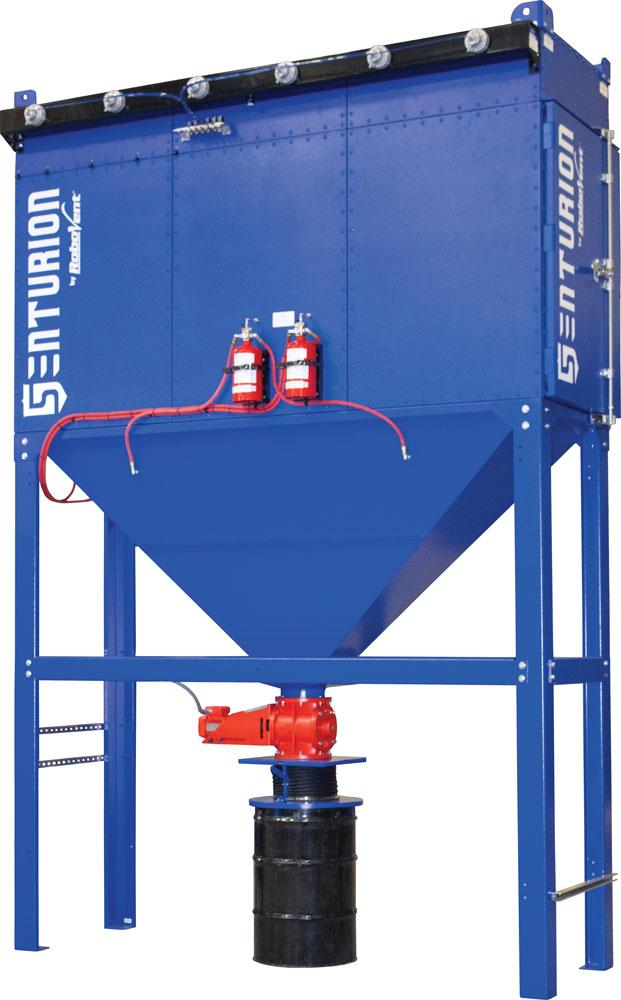
Comments
Post a Comment