- Get link
- X
- Other Apps
By
Jeffrey C. Nichols
-
A great article by
Chris Giusto at Hallam-ICS
This
blog outlines the process of completing a Dust Hazard Analysis (DHA) as
required by NFPA 652. The term DHA is often used interchangeably with
the “analysis” portion of the processes (Step 4 below), but a complete
DHA process involves additional steps before and after the analysis.
Blogs posts within this series:
The process outlined below assumes you have already determined that your facility manufactures, processes, or otherwise handles combustible dust. If you are not sure, refer to the section “Is My Dust Combustible” of my blog “A Practical Guide to 5 Important Properties of Combustible Dusts”.
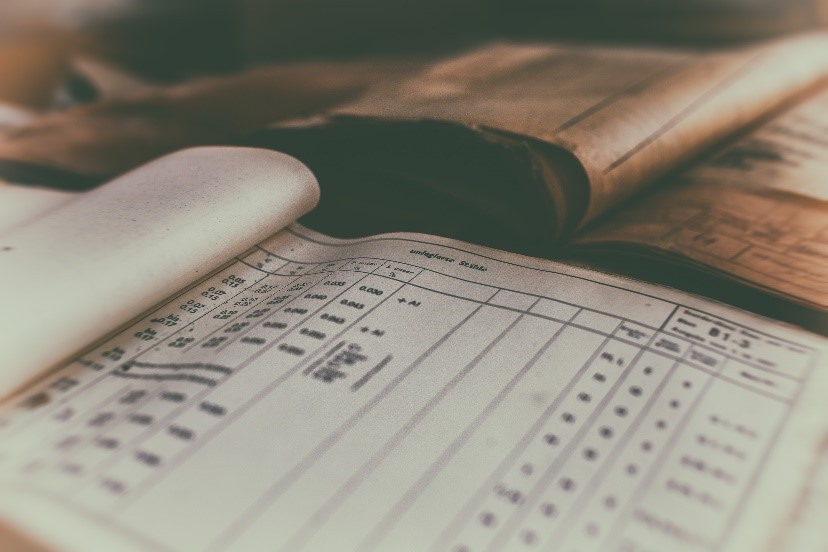
Documenting and understanding the materials involved in the process and their properties at each stage is also required. Most processes involve changes to a material’s properties such as size, particle size distribution (PSD), and moisture content, which all have a significant effect on how hazardous the dust is. If the dust has been tested to determine properties like Kst, Pmax, MEC, etc. copies of the test reports should be obtained and verified that they are representative of the various stages of any process where they might change.
The final set of documents required are the applicable NFPA standards. NFPA 652 provides guidance on the industry or commodity specific standards that may apply to your facility. Additional standards may also be applicable, but NFPA 68 Standard on Explosion Protection by Deflagration Venting and NFPA 69 Standard on Explosion Prevention Systems will likely be required reference for any facility.
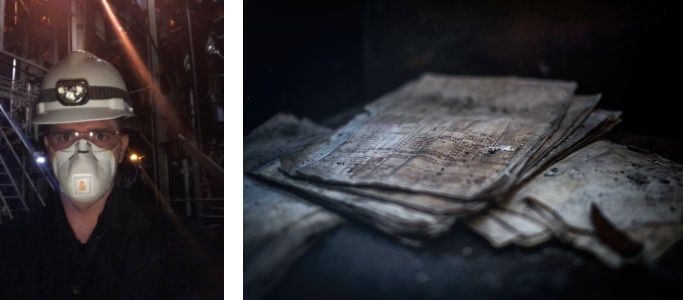
In instances where existing documentation is very limited, this step might be more appropriately titled “Field Survey.” Extensive efforts may be required to sufficiently document larger, older facilities to support a thorough DHA. This is a great opportunity for facilities that lack up-to-date PFDs to get their drawings revised (or recreated) to reflect the current state of the plant.
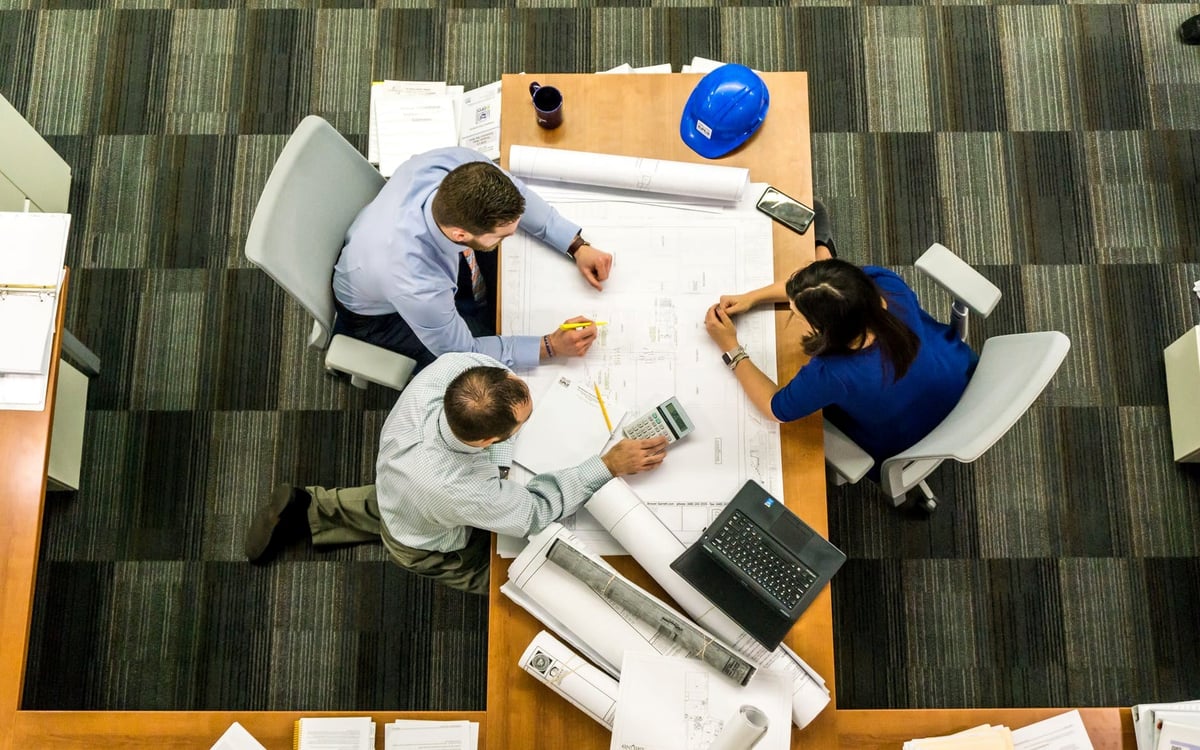
The perspective of a consultant who has been through the DHA process before can add tremendous value to your DHA. An outsider with experience in different facilities across a variety of industries might identify hazards and propose solutions your internal team members could overlook. To borrow a phrase from Dr. Chris Cloney, “You can’t read the label from inside the jar.”
There are different approaches and formats the team can use to facilitate this review, but the goal is the same: to consider every point in the process, identify hazards, and determine what measures are required to minimize the risks. It is helpful to remember the flash fire square (or quadrilateral) and explosion pentagon during this process. However, since air is usually the oxidizing agent, and you would not be conducting a DHA if you did not have combustible dust (fuel), the focus of the analysis tends to be on dust quantities/concentrations and ignition sources. For each step in the process and area of the facility, consider:
You
also want to identify any protective measures that are already in
place. If any hazards already have NFPA-compliant protection measures,
no additional action is necessary. It is equally important to identify
and document these measures in addition to the hazards. If measures are
installed, they should also be evaluated to confirm compliance with
NFPA standards.
For example, one facility I worked with had an explosion vent on an indoor dust collector that was vented through the roof. Initially this looked to be a good strategy to safely vent an explosion. Upon closer evaluation however, there was an improper weather cover over the vent duct, and the duct was not sized appropriately per NFPA 68. These issues created additional resistance that could have prevented the vent from functioning properly had there been an explosion. We determined the roof line was too far away from the top of the dust collector to install a complaint vent duct, and a flame arresting vent with particulate retention was installed instead.
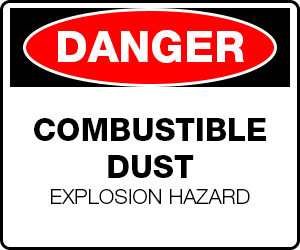
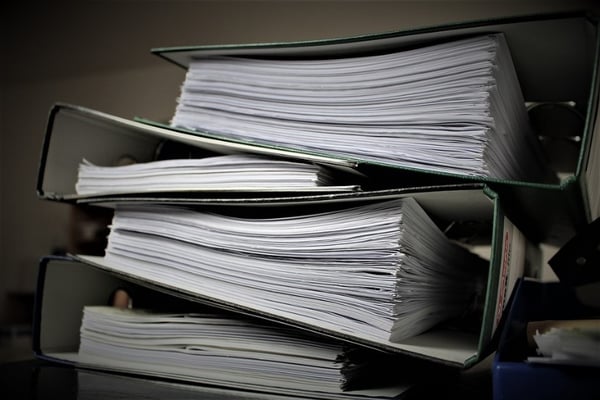
First, an Authority Having Jurisdiction (AHJ) can request to see the DHA. This could be a local fire marshal, an OSHA representative, or some other safety official. Having a complete and well-organized report shows that you are compliant with the relevant codes and standards, or that you have identified any areas that need attention and have a plan to address them.
Second, the DHA report serves as a reference for management of change as processes are modified and your facility goes through upgrades or growth. (I will discuss this topic more in a future blog as well.)
If you have questions or would like more information about DHAs and Combustible Dust Safety, you can contact Chris directly via email at cgiusto@Hallam-ICS.com.
About the Author
Chris Giusto is Director of Industrial Projects and works primarily with industrial facilities to improve processes & safety, reduce waste & energy consumption, increase flexibility & capacity, and build new facilities. He has nearly 20 years of mechanical engineering experience including design and specification of equipment and systems, detailed machine design, and project management. Areas of expertise include custom equipment design and fabrication, material handling, dust collection, and combustible dust safety.
Read My Hallam Story
Blogs posts within this series:
- Combustible Dust Fundamentals and NFPA 652
- What is a Dust Hazard Analysis (DHA)?
- A Practical Guide to 5 Important Properties of Combustible Dust
- 7 Steps to Complete a Dust Hazard Analysis
- I've Completed My DHA, Now What?
The process outlined below assumes you have already determined that your facility manufactures, processes, or otherwise handles combustible dust. If you are not sure, refer to the section “Is My Dust Combustible” of my blog “A Practical Guide to 5 Important Properties of Combustible Dusts”.
Step 1: Acquire Documentation
Begin by collecting any available relevant drawings and documents that define the process, equipment, operating parameters, or existing hazards. Examples of this include:- Process Flow Diagrams (PFDs)
- Piping and Instrumentation Diagrams (P&IDs)
- Mass & Energy Balance
- General Arrangement Drawings (GAs)
- Building Plans
- Equipment Manufacturer Drawings, Data Sheets, Manuals, etc.
- Electrical Hazard Classification Drawings
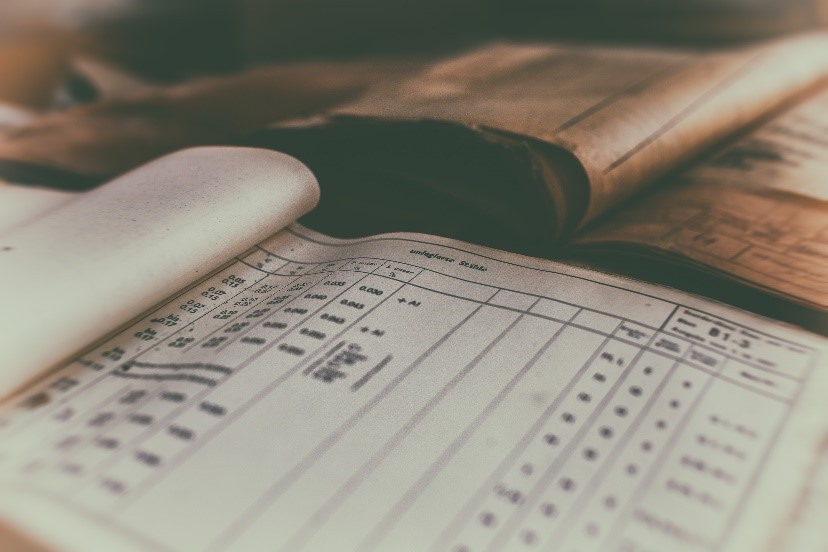
Documenting and understanding the materials involved in the process and their properties at each stage is also required. Most processes involve changes to a material’s properties such as size, particle size distribution (PSD), and moisture content, which all have a significant effect on how hazardous the dust is. If the dust has been tested to determine properties like Kst, Pmax, MEC, etc. copies of the test reports should be obtained and verified that they are representative of the various stages of any process where they might change.
The final set of documents required are the applicable NFPA standards. NFPA 652 provides guidance on the industry or commodity specific standards that may apply to your facility. Additional standards may also be applicable, but NFPA 68 Standard on Explosion Protection by Deflagration Venting and NFPA 69 Standard on Explosion Prevention Systems will likely be required reference for any facility.
Step 2: Field Verify
Even when the plant-specific documentation is available, it is frequently out-of-date or incomplete. The older the facility and existing documentation is, the more likely there have been undocumented changes. Due diligence should be exercised to verify the information that will serve as the basis for the DHA.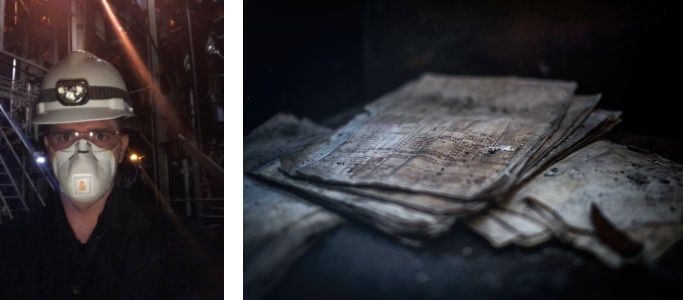
In instances where existing documentation is very limited, this step might be more appropriately titled “Field Survey.” Extensive efforts may be required to sufficiently document larger, older facilities to support a thorough DHA. This is a great opportunity for facilities that lack up-to-date PFDs to get their drawings revised (or recreated) to reflect the current state of the plant.
Step 3: Assemble DHA Team
NFPA 652 recommends (but does not require) that a DHA be completed by a team and requires that the DHA be led by a qualified person. (For more details on this, see the section “Who performs a DHA?” in “What is a Dust Hazard Analysis (DHA)?”). Assuming you take a team approach, plant engineers, environmental health and safety (EHS) personnel, and plant management all bring different perspectives and are frequently involved in the DHA process. Be sure to also consider including maintenance and operations personnel who often have hands-on experience that provides valuable insight to potential combustible dust hazards.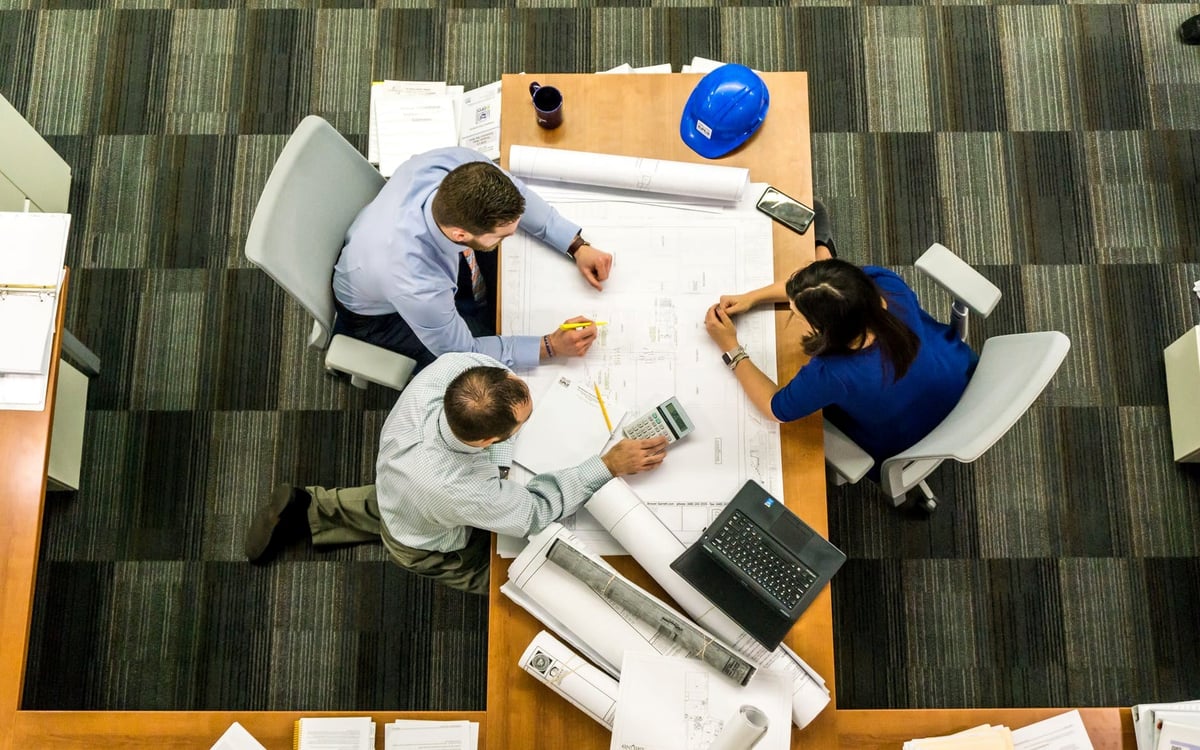
The perspective of a consultant who has been through the DHA process before can add tremendous value to your DHA. An outsider with experience in different facilities across a variety of industries might identify hazards and propose solutions your internal team members could overlook. To borrow a phrase from Dr. Chris Cloney, “You can’t read the label from inside the jar.”
Step 4: Identify Hazards & Evaluate Compliance
This step is the heart of the DHA—and the primary reason the process is mandated by NFPA 652. Many combustible dust incidents have been a result of hazards that owners and operators did not even know existed. This step is the part of the process where you systematically review and think critically about your process and facility to identify the potential hazards.There are different approaches and formats the team can use to facilitate this review, but the goal is the same: to consider every point in the process, identify hazards, and determine what measures are required to minimize the risks. It is helpful to remember the flash fire square (or quadrilateral) and explosion pentagon during this process. However, since air is usually the oxidizing agent, and you would not be conducting a DHA if you did not have combustible dust (fuel), the focus of the analysis tends to be on dust quantities/concentrations and ignition sources. For each step in the process and area of the facility, consider:
- Is there, or might there be, enough dust to produce a combustible atmosphere?
- Are there, or might there be, any means to disperse dust in a cloud?
- Are there, or might there be, any ignition sources?
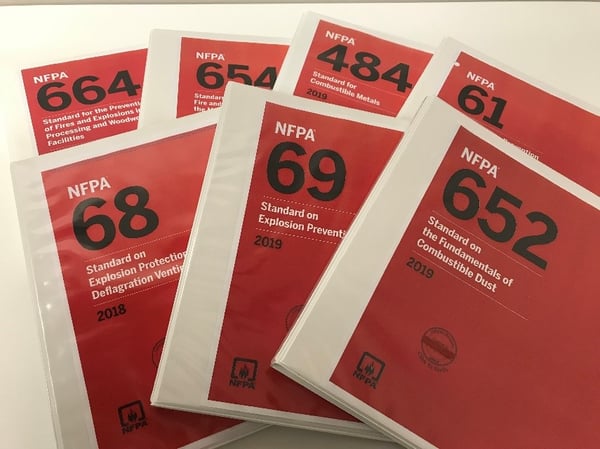
For example, one facility I worked with had an explosion vent on an indoor dust collector that was vented through the roof. Initially this looked to be a good strategy to safely vent an explosion. Upon closer evaluation however, there was an improper weather cover over the vent duct, and the duct was not sized appropriately per NFPA 68. These issues created additional resistance that could have prevented the vent from functioning properly had there been an explosion. We determined the roof line was too far away from the top of the dust collector to install a complaint vent duct, and a flame arresting vent with particulate retention was installed instead.
Step 5: Prioritize Hazards
Once the hazards are identified, the team must prioritize them so that the hazards presenting the greatest risk can be addressed first. As with Step 4, there are different approaches that can be used but some sort of risk matrix is usually employed to rank the hazards based on the anticipated likelihood that the event could happen and its anticipated severity. Some hazards may require immediate action, while others can be scheduled to be addressed at a future time. (I will cover this topic in greater detail in a future blog.)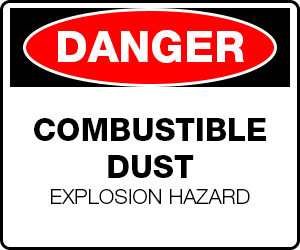
Step 6: Document Results
NFPA 652 requires that the results of the DHA be documented. Complete and thorough documentation are important for two primary reasons.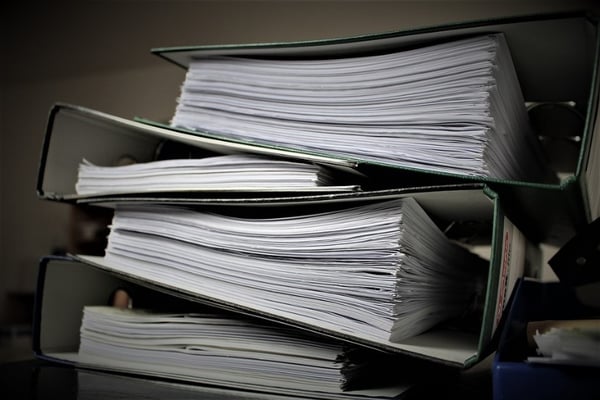
First, an Authority Having Jurisdiction (AHJ) can request to see the DHA. This could be a local fire marshal, an OSHA representative, or some other safety official. Having a complete and well-organized report shows that you are compliant with the relevant codes and standards, or that you have identified any areas that need attention and have a plan to address them.
Second, the DHA report serves as a reference for management of change as processes are modified and your facility goes through upgrades or growth. (I will discuss this topic more in a future blog as well.)
Step 7: Repeat
In facilities where combustible dust hazards have not previously been given adequate attention, completing a DHA will hopefully initiate a change in the organization from reactive compliance to proactive hazard management. The DHA needs to be revisited and updated as your facility undergoes changes. This includes changes to operating parameters of your existing processes, use of new or different materials or ingredients, installation of new equipment or processes, etc. In some facilities, this could happen several times per year, while others may go long periods without significant changes. To help ensure against complacency and the accumulative effects of unnoticeable changes, NFPA 652 section 7.1.4 requires the DHA to be reviewed and updated at least every 5 years.Summary
For plants with combustible dust, a Dust Hazard Analysis is essential to ensure the safety of your facility and personnel. This is why completing a DHA by September 7, 2020 is required by NFPA 652. I hope this information helps you understand the steps required to complete a DHA and reinforces the value of the process beyond just compliance.If you have questions or would like more information about DHAs and Combustible Dust Safety, you can contact Chris directly via email at cgiusto@Hallam-ICS.com.
About the Author
Chris Giusto is Director of Industrial Projects and works primarily with industrial facilities to improve processes & safety, reduce waste & energy consumption, increase flexibility & capacity, and build new facilities. He has nearly 20 years of mechanical engineering experience including design and specification of equipment and systems, detailed machine design, and project management. Areas of expertise include custom equipment design and fabrication, material handling, dust collection, and combustible dust safety.
Read My Hallam Story
About Hallam-ICS
Hallam-ICS is an engineering and
automation company that designs MEP systems for facilities and plants,
engineers control and automation solutions, and ensures safety and
regulatory compliance through arc flash studies, commissioning, and
validation. Our offices are located in Massachusetts, Connecticut, New York, Vermont and North Carolina and our projects take us world-wide.
Topics:
MEP Engineering,
Combustible Dust
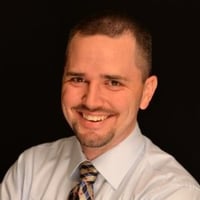
By
Chris Giusto
- Get link
- X
- Other Apps
Comments
Post a Comment